What is a relay?
A relay is a switch controlled by an electrical circuit in which one or more contacts are closed or opened, and in this way it closes or opens other electrical circuits that are independent.
Often the load connected to the output consumes more than the control that excites it or we want to electrically isolate both parts and it is for this reason that we need these devices named relays.
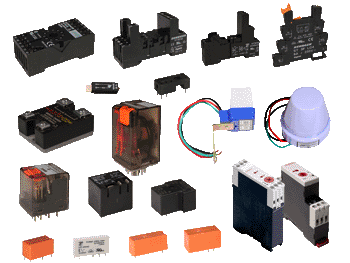
What are the basic classifications of relays?
-
Electromechanical based on a coil and an electromagnet that mechanically activates one or more contacts, closing or opening the circuits.
The classification of electromechanical relays is:
- Monostable: They are the most common and with a coil they close or open the circuits associated with them by applying the voltage to the coil.
-
- Bistable: These are relays that apply voltage to the coil and make the relay operate, but removing the voltage does not return it to the original position. We could say that they have interlocking. Frequently these types have two coils.
-
Solid state where the mechanical elements are replaced by a semiconductor electronic circuit. The switching time, not being mechanical, is practically instantaneous, and makes them ideal for switching inductive loads or in those circuits where the activation and deactivation of the relay is carried out frequently.
What are the main parameters of a relay?
The parameters of a relay are:
Determine basic issues as with any object: size, weight and physical shape:
-
-
Length.
-
Broad.
-
Height.
-
Diameter.
-
Weight.
-
Physical form.
-
Parameters of a relay depending on its contacts and circuits
It is the maximum current that the relay can withstand safely and without being damaged when opening and closing its contacts.
Defines the configuration of the circuits, relay poles and throws and its behavior. The basic information are:
-
-
- The pole is the input of the circuit breaker.
- The number of poles will define the number of individual circuits that the relay can manage.
- The throws that each relay circuit has.
The contact forms of a relay are defined by:
-
-
- Format : The configuration of the relay based on its poles, circuits and outputs.
Its encoding is determined using the following format:
-
-
-
- (Number of poles) P (Number of throws) T
-
- The number of poles and throwscan be defined with a letter or a number: S - Single or 1 pole, D - Double or 2 poles, 3 - 3 poles and so on. The most common classifications are:
-
-
-
- SPST (Single Pole Single Throw): It is the simplest, a switch with 1 input and 1 throw.
-
- SPDT (Single Pole Double Throw): It is a switch with 1 input and 2 throws.
-
- DPDT (Double Pole Doble Throw): 2 poles and therefore 2 circuits, 2 throws per circuit.
-
- 3PDT (3 Poles Doble Throw): 3 poles and therefore 3 circuits, 2 throws per circuit.
-
- 4PDT (4 Poles Doble Throw): 4 poles and therefore 4 circuits, 2 throws per circuit.

-
-
- Form: Defines the behavior of the relay circuits when it is stopped and when it comes into operation. The magnetic field is generated by the relay coil after applying its working voltage, or by an external magnetic field in Reeds relays.
Its encoding is determined using the following format:
-
-
-
- [Number of poles] Form (x)
The number of poles is an optional data depending on the manufacturer. If the information has been included in the form, the number of poles may not be included in the form.
The defined forms are:
-
-
-
- A: NO - Normally Open Contacts when the relay coil is stopped or de-energized, or when there is no nearby magnetic field in the case of Reed relays.
-
- B: NC - Normally Closed Contacts when the relay coil is stopped or de-energized, or when there is no nearby magnetic field in the case of Reed relays.
-
- C: Contacts Normally Open in one circuit and Normally Closed in another when the relay coil is stopped or de-energized, or when there is no nearby magnetic field in the case of Reed relays.
-
- In type C, at the moment of the coil's ignitioning, the circuit that is Normally Closed when is stopped or de-energized then will become open, and then once the start of ignition time has elapsed, the circuit did not change its state and was open, it will be closed.
-
- Form C guarantees that for an instant, all contacts are open (BBM - Break-Before-Make).
-
- D: It is similar to Form C except for the behavior of the ignition time. In Form C, at the moment the coil starts to work, all the contacts will be closed. (MBB - Make-Before-Make).

-
Parameters in relation with relay coil
It is the nominal voltage at which the coil is designed to operate.
Minimum voltage determined by the manufacturer, and is the one required for the electromagnet to start operating due to the magnetic effect generated by the coil, without altering other parameters such as the activation time.
Maximum voltage determined by the manufacturer, which can be applied to the coil in the usual way without being damaged.
-
-
Voltage type or current type
Type of voltage that can be applied to activate the relay:
-
-
- Vac: Designed for alternating current.
- Vdc: Designed for direct current.
- Vac / Vdc: Designed for operation in both alternating current and direct current.
-
Coil resistance
The internal resistance of the coil.
It refers to the coil consumption.
What are bounces in an electromechanical relay?
Bouncing in an electromechanical relay refers to temporary, intermittent oscillations in the connection and disconnection of the relay contacts when the relay coil is energized or de-energized. These oscillations can occur during the switching process of the relay contacts and are caused by the mechanical nature of the relay's internal moving components such as the contacts and spring.
When the relay coil is energized, it creates a magnetic field that attracts the magnetic core, moving the contacts to close the electrical circuit. Similarly, when the coil is de-energized, the contacts return to their original position opening the circuit. During these movements, bouncing may occur due to spring elasticity and mechanical tolerances in internal components.
What are the problems associated with electromechanical relay bounces?
Bouncing can cause electrical interference or noise in the circuit, which can negatively affect other nearby electronic components.
The presence of bouncing can accelerate the wear of the relay contacts, potentially reducing its useful life.
In applications where accuracy and stability are critical, bouncing can cause problems in control circuits, such as erroneous readings or malfunctions.
How can the contact bounce of an electromechanical relay be reduced?
Reducing relay contact bounce is crucial to ensuring accurate and stable operation in critical applications.
Strategies that can be used to minimize contact bounce in an electromechanical relay:
Circuit Debouncing
- Decoupling Capacitors : Adding capacitors in parallel to the contacts can help absorb oscillations during closing and opening of the relay.
- Load resistors: Introducing resistors in series with the contacts can reduce the speed of change and minimize bounces.
Use of diodes (suppression diodes)
- Avalanche diodes: Placing an avalanche diode in parallel with the relay coil can help reduce bouncing by providing a path for reverse current.
Advanced control systems
- Microprocessor control: Employ microprocessor-based control systems that incorporate filtering and timing algorithms to manage bounces.
- Adjustable timing: Allow adjustments to relay timing to suit specific application characteristics.
High quality contacts
- Low-burr contacts: Use high-quality relay contacts designed to minimize the formation of burrs that can cause bouncing.
Gold contacts or special materials
- Gold-Plated Contacts: Contacts that are gold-plated or made of special materials can help reduce oxide formation and improve conductivity, thereby decreasing the chance of bouncing.
Proper coil drive
- Stable voltage and current: Providing stable voltage and current to the relay coil can help reduce bouncing.
Regular maintenance
- Cleaning and lubrication: Performing regular maintenance, including cleaning and lubricating moving components, can help reduce bouncing.
To comment the application of these techniques may depend on the specific application and relay design. Additionally, in some cases, it may be beneficial to combine several strategies to achieve effective bounce reduction.
Types of relays that you can find in Electronica Embajadores
Miniature Electromechanical Relays: They are electromechanical relays for low signal, generally used in telecommunications and/or switching of small loads.
Conventional Electromechanical Relays: These are general purpose electromechanical relays of small case, and approximately up to 10 A.
Medium Power Electromechanical Relays: These are general purpose electromechanical relays of larger case than miniature ones, and approximately up to 20 A.
High Power Electromechanical Relays: They are also electromechanical relays and above 20 A. An example of this type of relay is those commonly used in the automotive industry with faston connection terminals.
Accessories & Sockets for Relays: When we want to install a relay in an electrical panel, or we have to quickly extract the relay from the system to which it is connected, we resort to relay sockets. These and other accessory devices for the relays are what you will find in this section.
Telephone Relays: It is a particular type of relay that is excited by the voltage of the telephone call. They also have connection terminals.
Reed Relays: It is a switch or switch that is activated by a magnetic field. When the contacts are normally open they close in the presence of a magnetic field; When normally closed they open in the presence of a magnetic field. There are also switched ones.
Solid State Relays: These are relays that do not have mechanical processes for their movement as they lack a coil and an electromagnet. These relays use semiconductor elements to perform switching, such as thyristors, triacs, diodes and transistors.
Timer Relays: Timer relays are not electronic components. A timer relay is a system that allows the circuit to be switched through an established timing, in such a way that there are cyclical relays, connection delays, that deliver a pulse, etc. Even multifunction in which we can set the specific timer and time function.
Twilight Relays: These relays are not electronic components. These relays are systems that activate and deactivate automatically depending on the existing brightness. Common functions may be the automatic turning on and off of a streetlight depending on the existing brightness.