Waterproof enclosures are key components in protecting electronic equipment against adverse environmental factors such as dust, humidity, corrosion and physical impacts. They are designed to ensure the integrity and safe operation of the devices they contain, even in hostile environments.
These boxes are designed with high-quality plastic materials, offering a unique combination of durability, strength and lightness. Its robust construction ensures protection against impacts, vibrations and adverse environmental conditions, while its light weight makes it easy to handle and transport.
The most notable feature of these boxes is their ability to provide an airtight seal, making them the ideal choice for environments where moisture, dust, dirt or chemicals could compromise the functionality of electronic components. Thanks to their waterproof design, these boxes protect printed circuits, connectors, and other internal elements from the infiltration of liquids or foreign particles, thus prolonging the useful life of electronic devices and reducing the need for maintenance.
Materials used in waterproof plastic boxes
Here we will talk about some of the plastic materials commonly used in the manufacture of these waterproof boxes and their main characteristics:
Waterproof ABS (Acrylonitrile Butadiene Styrene) boxes:
- It is a thermoplastic polymer known for its impact resistance and good toughness.
- ABS is easy to shape, making it a popular choice for watertight enclosures that require specific shapes or custom designs.
- It has good chemical and abrasion resistance, making it suitable for a variety of environments.
Waterproof PC (Polycarbonate) boxes:
- It is a durable plastic with excellent optical transparency and impact resistance.
- Waterproof PC cases are ideal when high visual clarity is needed to inspect the equipment inside the case without opening it.
- They have good thermal and UV resistance, making them suitable for outdoor applications.
Enclosures made of EPS (Expanded Polystyrene):
- EPS is a lightweight and low-cost material, known for its excellent thermal insulation properties and impact absorption.
- Although it is not commonly used in enclosures for industrial or demanding environments, it can be useful in applications requiring insulation and lightness.
- It is moisture-resistant, but its relative fragility makes it less suitable for environments where high durability or mechanical strength is needed.
Enclosures made of HIPS (High Impact Polystyrene):
- HIPS is a tougher variant of polystyrene, offering greater toughness and impact absorption capability.
- It is easy to mold and is used in applications where good impact resistance and affordability are required.
- HIPS enclosures are suitable for low to medium-demand environments, offering a good balance between cost, durability, and impact resistance.
Enclosures made of GRP (Glass Reinforced Polyester):
- GRP is a highly resistant composite material, formed by a polyester matrix reinforced with glass fibers.
- It is known for its high mechanical strength, excellent rigidity, and corrosion resistance, making it ideal for use in aggressive industrial environments.
- GRP enclosures are extremely durable, capable of withstanding strong impacts, extreme environmental conditions, and prolonged exposure to chemicals. This makes them an ideal choice for industrial, marine, or demanding outdoor applications.
Nylon waterproof boxes:
- It is a thermoplastic polymer that belongs to the polyamide family. It is known for its strength, durability and low friction.
- Nylon waterproof cases are lightweight and have good chemical and impact resistance.
- They are suitable for applications requiring resistance to abrasion and fatigue.
Waterproof Polyamide 66 (PA66) boxes:
- PA66 is a specific type of polyamide that is derived from the polymerization of adipic acid and hexamethylenediamine.
It is known for its excellent mechanical strength, rigidity and heat resistance.
- PA66 is commonly used in applications that require high strength and dimensional stability, such as electronics waterproof boxes.
- It also has good resistance to abrasion and chemicals, making it suitable for demanding industrial environments.
Waterproof Polyamide 6 (PA6) boxes
- PA6 is a polyamide that is manufactured by the polymerization of caprolactam, a monomer with six carbon atoms.
- It is known for its good mechanical resistance, rigidity and toughness.
- It has excellent impact resistance, making it suitable for applications where high durability is required, such as waterproof boxes for electronics.
- PA6 also exhibits good abrasion and chemical resistance, making it useful in industrial and outdoor environments.
- PA6 shares some characteristics with nylon (polyamide), but has some differences in terms of specific properties and processing. However, like nylon, PA6 is a versatile material and widely used in various applications, including waterproof enclosures for electronics.
Elastomers and rubber derivatives:
- Elastomers, such as silicone rubber or ethylene propylene rubber (EPDM), are used for seals and gaskets in waterproof boxes to provide additional protection against the ingress of water and dust.
- They are flexible and have a high sealing capacity, ensuring the tightness of the box even in adverse conditions.
Blends of different materials:
- Fiberglass is often added to polycarbonate enclosures to increase their strength, or also to those made of epoxy resin, nylon, or polyester, for example, as is the case with GRP, which we have already discussed.
- Sometimes, the goal is to give the enclosure a pleasant feel, so a thin layer of elastomer material is added to the enclosure, whether it is made of ABS or another material.
These plastic materials offer a variety of physical and chemical properties that make them suitable for different applications and environments. Choosing the appropriate material will depend on factors such as the application environment, mechanical strength requirements, exposure to chemicals, and the need for visual transparency, among others.
What is IP grade?
The IP (Ingress Protection) rating system or IP protection grade establishes levels of protection against particles and water for electronic equipment. For the first digit, which represents the tens, the levels of protection against particles are defined, from 0 (no protection) to 6 (full protection against dust). For the second digit, which represents the units, the levels of protection against water intrusion are defined, from 0 (rapid entry of water) to 9K (protection against high pressure and temperature jets). For example:
IP65 indicates complete protection against dust (6) and non-pressurized water jets (5).
IP67 means dustproof (6) and complete immersion in water for up to 30 minutes (7).
IP68 indicates protection against dust and continuous immersion in water.
It is important to consider the manufacturer's specifications to understand the true immunity of the equipment under specific conditions.
The different degrees of IP protection are defined more completely in the previous link. However, we consider that a box can be called watertight from an IP54 level, although practically all the boxes that we present in this section usually have indices equal to or greater than IP65. We do not publish boxes with ratings lower than IP54 in this category.
In addition to protecting the internal elements that go inside the box, we must protect the external components or parts that may be affected by dust and water. For all this, the degree of protection also applies to the rest of the elements. We understand that if we use a waterproof box and we have to place a button, a cable gland or a connector in said box, for example, these elements must have the necessary IP protection. And that is why we have made a general compilation with filters, for easy location, of all those components from different categories with IP grades that we consider watertight. See waterproof products.
Combustibility degree
As a plastic material, plastic waterproof boxes are also classified by their degree of combustibility, or the degree of combustibility due to the material with which they are made.
The combustibility rating is a measure of a material's ability to burn or spread fire when exposed to an ignition source. It is used to evaluate the flammability of materials and is especially relevant in applications where fire safety is a concern, such as in the manufacture of waterproof boxes for electronics. Here are some considerations about the flammability rating in relation to watertight boxes:
- Regulations and standards:
- In many countries, there are regulations and standards that establish minimum flammability requirements for materials used in electronic products and other devices.
- For example, in the United States, the UL 94 standard establishes the criteria for classifying the flammability of plastic materials used in electrical and electronic equipment.
- Flammability Ratings:
- The UL 94 standard classifies plastic materials into different flammability categories based on their ability to extinguish flame and resist the spread of fire.
- Common ratings include V-0, V-1, and V-2, with V-0 representing the highest level of flammability resistance and V-2 the lowest level.
- Materials selection:
- For electronics waterproof enclosures, it is important to select materials that meet the appropriate flammability requirements for the application.
- Materials with a higher flammability rating, such as V-0 per UL 94, provide greater fire safety and may be preferable in environments where fire prevention is crucial.
- Additional considerations:
- In addition to flammability rating, other factors such as mechanical strength, chemical resistance, and dimensional stability are also important when selecting materials for watertight boxes.
- Compliance testing with specific standards and safety certifications may be required to ensure that watertight enclosures meet applicable safety and regulatory requirements.
In summary, combustibility rating is an important consideration when selecting materials for electronics enclosures, as it helps ensure fire safety and compliance with applicable safety standards. It is essential to choose materials with the appropriate flammability classification for the specific application and to comply with relevant regulations and standards.
What is ATEX?
Some of our boxes for electricity or electronics comply with ATEX regulations. But what is ATEX?...
ATEX is the abbreviation for “ATmosphères EXplosives” (Explosive Atmospheres). At the same time, it refers to a safety standard, a set of European Union directives that regulate all equipment installed in potentially explosive atmospheres (both gas and dust).
- Directive 2014/34/EU (formerly known as 94/9/EC): This directive refers to equipment and protective systems intended for use in explosive atmospheres. It includes product certification and establishes the essential requirements that manufacturers must meet to ensure the safety of this equipment.
- Directive 1999/92/EC (also known as "ATEX 137"): This regulates the safety of workers operating in zones with explosion risks. It defines the employer's responsibilities, such as classifying hazardous areas and adopting measures to reduce or eliminate the risk of explosions.
ATEX harmonizes various technical and legal requirements at the national level in Europe to ensure a very high level of safety.
The objective of Directive 2014/34/EU is to allow the free trade of ‘ATEX’ equipment and protection systems within the EU, eliminating the need for separate testing and documentation for each member state.
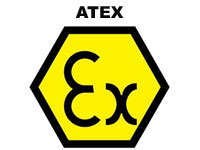
How is a potentially explosive atmosphere defined according to ATEX?
An explosive atmosphere is a mixture of flammable substances in the form of gases, vapors, mists, or dusts with air under atmospheric conditions, where, after ignition, combustion spreads to the entire unburned mixture.
An atmosphere that could become explosive due to operational conditions is called a Potentially Explosive Atmosphere.
Classification of explosive atmospheres
|
Category |
Atmosphere |
Zones |
Presence of Explosive Atmosphere |
Group I (Mining Industries)
|
M1 |
Gas and Dust
|
Equipment will be energised |
M2 |
El equipo será desenergizado |
Group II (Surface Industries)
|
1 |
Gas |
0 |
Always |
Dust |
20 |
2 |
Gas |
1 |
Occasionally |
Dust |
21 |
3 |
Gas |
2 |
Rarely |
Dust |
22 |
Areas of ATEX application
ATEX applies to industries that work with gases, vapors, dust, or flammable materials, such as sectors like:
- Petrochemicals
- Refineries
- Mining
- Chemical industry
- Food industry (in cases of flammable dust)